Finding Talent When Those Interested in Working Is at a 45-Year Low
The number of unfilled manufacturing jobs during the initial months of 2021 has not been higher since the Great Recession. During most months since October 2020, the number of unfilled manufacturing jobs has exceeded 500,000. For reference, during the last business cycle of 2017-2020, the average number of unfilled manufacturing jobs was 430,000. During only two months of that cycle did unfilled openings barely reach 500,000.
Stimulus checks, deficit government spending, debt and rent payment forgiveness and/or suspension and a re-opening of many of the industries that were crippled by the pandemic have created swelling demand for goods and services. Promoting consumer demand was and continues to be an essential part of America — and the world’s — economic recovery as evidenced by U.S. GDP growth of 6.4% during 1Q2021.
Although demand-side efforts to bolster the economy have been strongly effective, economic growth has been stymied by a lack of products to sell to willing consumers. Dissimilar to prior economic slowdowns, the regulatory shutdown of businesses in early 2020 meant that inventory-to-sales ratios didn’t swell as they typically do early in a recession, meaning that the world economy is rebounding with far lower levels of pre-existing inventory on shelves. Furthermore, supply chains have struggled to resume normal operations due to an unfortunate string of unrelated one-off events including weather, building fires and blocked shipping canals, to name a few. Frequently, such one-off events usually have only temporary impacts and are quickly overcome, but the recent string of such events at a time when inventories were already depleted has made the situation much worse.
Despite the challenges associated with these one-off events, the greatest supply-side challenge is and will continue to be the limited participation of the labor force. At present, the U.S.’ labor force participation rate at just over 61% is at a low last seen in 1976.
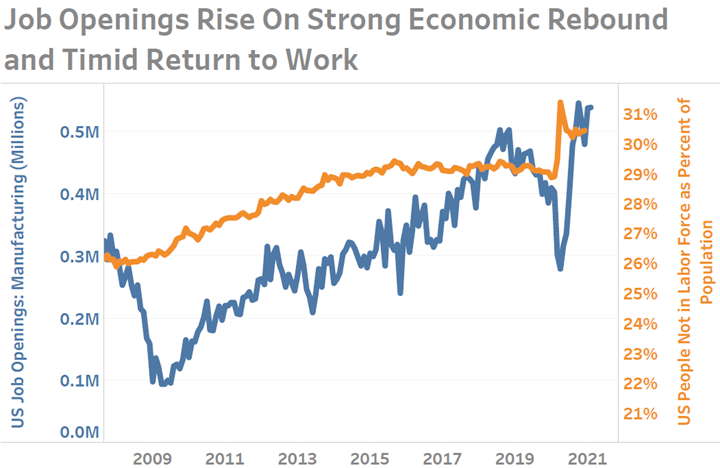
The percent of people NOT in the labor force has reached a high last seen in the mid-1970s. At present, the reasons for the lack of participation are many. However, there are things that ambitious companies that are willing to think outside-the-box can do to fulfill their labor needs.
Many will be quick to point to generous stimulus payments and welfare programs as evidence that people would rather receive “free” money than — in some instances — receive less money by working (who wouldn’t?!). As evidence of this, an April 2021 Federal Reserve paper reported that many unemployed are being more selective than usual when considering job offers thanks to Government efforts to reduce the pandemic’s financial pressure on families. However, there are also many other reasons for this low participation rate that can be solved by creative business leaders. Prospective employees continue to cite a fear of getting COVID-19, childcare needs, and caring for elderly family members as reasons for not seeking a job.
Focusing on these later concerns, manufacturing leaders should ask themselves: what can they do to bring down these barriers to employment? If your firm was to provide direct or indirect support for childcare, or greater work flexibility for employees with elderly or at-risk family members, would the additional costs of such programs be more than offset by having employees who clearly realize that you are willing to help them meet their very real and personal needs and are thus strongly motivated and dedicated? Prior to the pandemic — when I was speaking around the country and world — I heard amazing success stories from manufacturing leaders who would take special risks on new employees. In these situations, the new employees clearly understood their good fortune to have a new job that was to some degree tailored to their personal situation. In the outstanding cases, this special work relationship deeply motivated the new employees to perform at their best and in some instances become the company’s star performer. Once again, manufacturing leaders need to draw on those creative past experiences to resolve this most critical of all their supply-side challenges. While one-off events capture headlines, none of them are as significant as the structural labor force problems which have only worsened over decades.